Products > Thread cutting technology > Cold-Forming Taps
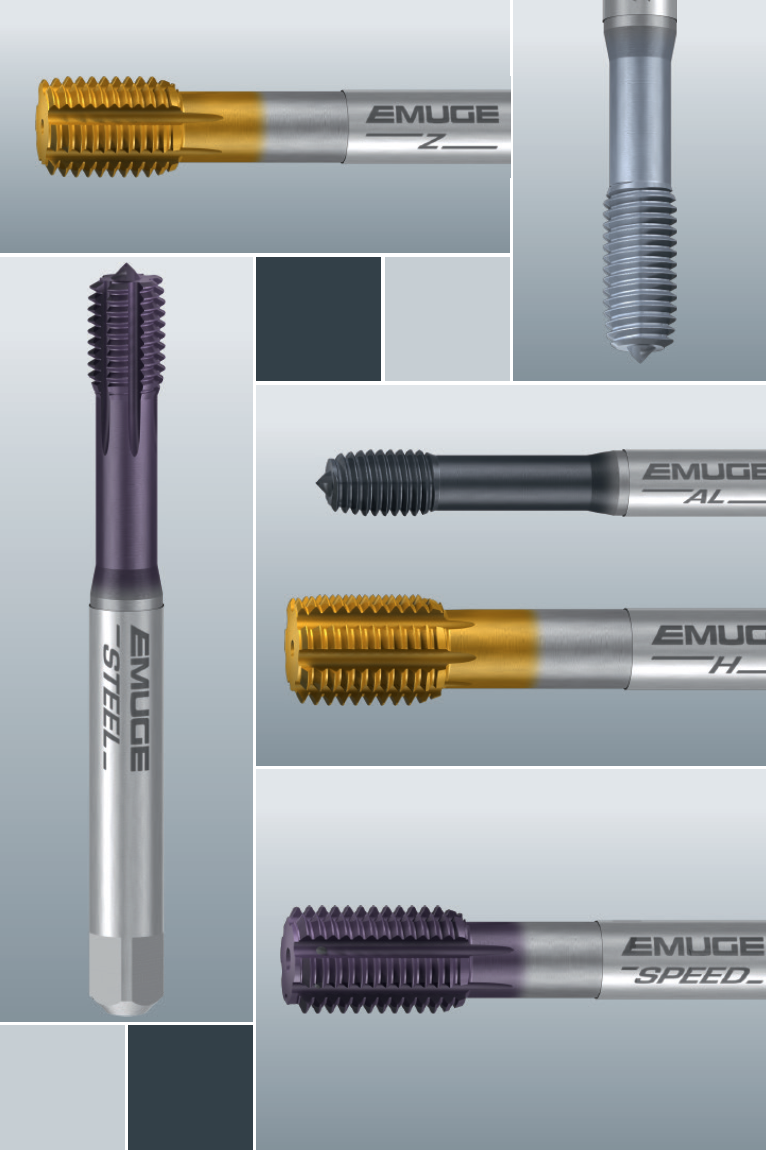
In the right application, thread forming can boost quality and throughput
The vast majority of threaded holes–more than 90%, according to one supplier of taps and other cutting tools–are produced using cutting taps.
But many of those threads could be produced using forming taps, which can provide multiple advantages. For ductile work materials, thread forming can provide better size control and stronger threads while improving tool life and productivity.
Unlike thread cutting, no material is removed during thread forming. Rather, the process displaces the material to generate the thread form. Since the metal’s structure is cold worked along the thread profile, the threads produced are generally stronger and have a smooth, burnished surface finish.
Forming taps must be applied in materials that cold form well. This includes light metals and light metal alloys as well as steels and other materials with tensile strength to 1200 N/mm2 and hardness below about RC 35 – 40. Generally, materials that produce a continuous chip when drilling are good candidates for thread forming. This list is longer than you might think, and includes wrought and cast aluminum and aluminum alloys, copper, brass, stainless steels, carbon steels, and zinc diecasting alloys.